Showing 3 results for Shafaei
A. Azizi, S. Z. Shafaei, M. Noaparast, M. Karamoozian,
Volume 10, Issue 4 (december 2013)
Abstract
This paper was aimed to address the modeling and optimization of factors affecting the corrosive wear of low alloy and high carbon chromium steel balls. Response surface methodology, central composite design (CCD) was employed to assess the main and interactive effects of the parameters and also to model and minimize the corrosive wear of the steels. The second-order polynomial regression model was proposed for relationship between the corrosion rates and relevant investigated parameters. Model fitted to results indicated that the linear effects of all of factors, interactive effect of pH and grinding time and the quadratic effects of pH and balls charge weight, were statistically significant in corrosive wear of low alloy steel balls. The significant parameters in the corrosive wear of high carbon chromium steel balls were the linear effects of all factors, the interactions effect of solid concentration, mill speed, mill throughout, grinding time, and the quadratic effects of pH and solid content. Also, the results showed that within the range of parameters studied, the corrosion rate of 78.38 and 40.76 could be obtained for low alloy and high carbon chromium steel balls, respectively.
A. Azizi, S.z. Shafaei, R. Rooki,
Volume 13, Issue 2 (June 2016)
Abstract
Nowadays steel balls wear is a major problem in mineral processing industries and forms a significant part of the grinding cost. Different factors are effective on balls wear. It is needed to find models which are capable to estimate wear rate from these factors. In this paper a back propagation neural network (BPNN) and multiple linear regression (MLR) method have been used to predict wear rate of steel balls using some significant parameters including, pH, solid content, throughout of grinding circuit, speed of mill, charge weight of balls and grinding time. The comparison between the predicted wear rates and the measured data resulted in the correlation coefficients (R), 0.977 and 0.955 for training and test data using BPNN model. However, the R values were 0.936 and 0.969 for training and test data by MLR method. In addition, the average absolute percent relative error (AAPE) obtained 2.79 and 4.18 for train and test data in BPNN model, respectively. Finally, Analysis of the predictions shows that the BPNN and MLR methods could be used with good engineering accuracy to directly predict the wear rate of steel balls.
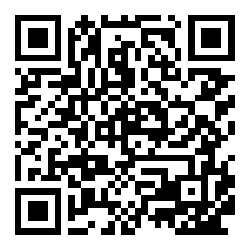
Yaser Moazzami, Mahdi Gharabaghi, Ziadin Shafaei Tonkaboni,
Volume 19, Issue 4 (Desember 2022)
Abstract
Ionic liquids as green solvents with high thermal stability, recyclability, low flash point, and low vapor
pressure, have been considered as a viable alternative in hydrometallurgical processes. In this study the leaching
kinetics of chalcopyrite concentrate was investigated using 1-Butyl-3-methylimidazolium hydrogen sulfate
(BmimHSO4) as an acidic ionic liquid. The Effect of operational parameters, including temperature, BmimHSO4
concentration, H2O2 concentration, stirring speed, solid-to-liquid ratio, and particle size on the rate of copper
dissolution of CuFeS2 were examined systematically. The highest Cu efficiency (ca. 97%) was achieved using 40%
(w/v) BmimHSO4, 30 %v/v H2O2, and 10 g.L-1 solid to liquid ratio for particle sizes less than 37 μm at 300 rpm and
45°C after 180 min leaching time. Kinetics study using Shrinking Core Model (SCM) revealed that CuFeS2 leaching
process using BmimHSO4 follows chemical reaction-controlled process. Under these circumstances, the calculated
activation energy was 46.66 KJ/mol. Moreover, the orders of reaction with respect to BmimHSO4 and H2O2
concentration, solid to liquid ratio and particle size were estimated to be 0.539, 0.933, −0.676 and −1.101
respectively. The obtained Arrhenius constant was found to be 0.26 106. The calculation of apparent activation
energy using “time given to a fraction method” revealed that the leaching mechanism remains the same over the
course of time.