Showing 4 results for Metakaolin
M. A. Soleimani, R. Naghizadeh, A. R. Mirhabibi, F. Golestanifard ,
Volume 9, Issue 4 (12-2012)
Abstract
Metakaolinite-based geopolymer has been synthesized at about 25 °C from metakaolin which has been calcined in different temperatures (600-900 °C) and different Na2O/SiO2 ratio activator (0.3-1.1). Compressive strength and microstructure of cement pastes after 7-28 days curing at ambient temperature were measured. Compressive strength tests on the samples showed that the sample made with calcined kaolin at 700 °C and molar ratio of 0.6 has highest average compressive strength of 32 MPa after 28 days of curing. Evaluation of infrared spectroscopy (FTIR) and microstructure showed that geopolymer cement developed and new molecular structure established
H. R. Sobhani Kavkani, A. Mortezaei, R. Naghizadeh,
Volume 13, Issue 2 (6-2016)
Abstract
Different mineral admixtures of Indian metakaolin, Iranian silica fume and nanosilica were used to produce high performance mortars. Two different sands types with grain size of 0.015-4mm were mixed with type II Portland cement, polycarboxylate superplasticizer,mineral admixture with 650kg/m3 cement content and water/cement ratio of 0.35. Different amount of cement was replaced by metakaolin or silica fume (5-15wt%) or nanosilica (0.8-5wt%). After mixing, moulding and curing, compressive strength, electrical resistivity and abrasion resistance were studied. The maximum compressive strength of 28 days samples were 76MPa, 79MPa and 75MPa for 15wt% substitution of cement with metakaolin, silica fume and 5wt% with nanosilica. The compressive strength of these samples showed 28%, 33% and 26% increment in comparison with reference sample, respectively. X-ray patterns showed that replacing silica fume leads to reduction of Portlandite (Ca(OH)2) phase. This can be attributed to the pozzolanic reaction and formation of new hydrated calcium silicate phase (CSH) that caused improvement of strength of admixtures containing samples. The microstructure of silica fume containing sample also showed better bond between sand and matrix. The electrical resistivity of samples with 15wt% metakaolin or silica fume and 5wt% nanosilica reach to 21kΩ.cm, 15 kΩ.cm and 10kΩ.cm, respectively. These samples showed high durability and corrosion resistance relative to reference samples (3.4 kΩ.cm). The abrasion resistance of different admixtures, specially silica fume containing samples were improved.
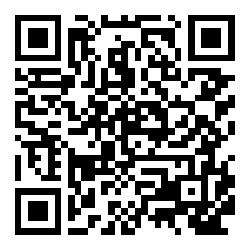
Ekaterina Dmitrieva, Ivan Korchunov, Ekaterina Potapova, Sergey Sivkov, Alexander Morozov,
Volume 19, Issue 4 (12-2022)
Abstract
The article discusses the effect of calcined clays on the properties of Portland cement. An optimal method for calcining clays is proposed, which makes it possible to reduce the proportion of Portland cement clinker in cement to 60% and increase the strength characteristics from 55 MPa to 79 MPa. The study of the composition and structure of clays made it possible to select the optimal heat treatment parameters, at which the calcination products are characterized by the highest pozzolanic activity. It is shown that the use of alkali-activated calcined clays significantly increases the strength and durability of hardened cement binders compared to the composition without additives. In addition, calcined clays increase the frost resistance of cement in a 5% NaCl solution. The obtained experimental data are confirmed by thermodynamic calculations and the results of scanning electron microscopy.
Nailia Rakhimova, Vladimir Morozov, Aleksey Eskin, Bulat Galiullin,
Volume 20, Issue 3 (9-2023)
Abstract